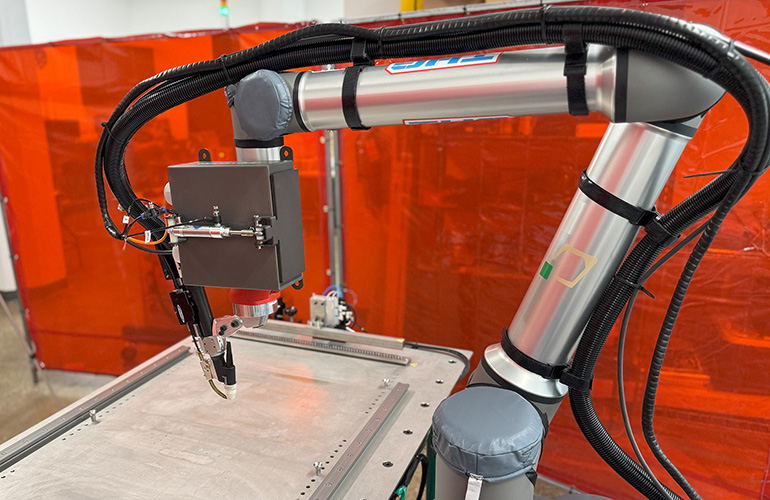
The Smart Welding Robotic Workcell is designed to perform multiple production tasks. Source: Cohesive Robotics
Cohesive Robotics Inc. this week announced the availability of the Smart Welding Robotic Workcell, its latest automation using artificial intelligence to support manufacturers. The company said the new offering is designed to address critical fabrication bottlenecks, boost production capacity, and improve accuracy for customers.
“We’re laser-focused on helping manufacturers of all sizes adopt the very best in automation capabilities to boost their production, address labor shortages, and remain competitive,” stated David Pietrocola, co-founder and CEO of Cohesive Robotics. “With our Smart Welding Robotic Workcell joining our product lineup, we can now better support upstream processes and provide a unified automation framework for our customers.”
Cohesive Robotics said it develops and deploys “smart turnkey robotic workcells” for operations in construction, aerospace, and other industries. The company claimed that its Argus OS proprietary software and AI system can help manufacturers avoid costly and time-consuming robot programming and integration, reduce rework and waste, and address workforce challenges.
Brooklyn, N.Y.-based Cohesive Robotics is a member of the New York Robotics Network.
Smart Welding Workcell can perform varied processes
Argus OS uses 3D scans and AI to automatically identify parts and program industrial and collaborative robots to perform a variety of common processes in high-mix and high-variability production environments. It integrates this technology into application-specific autonomous workcells such as the Smart Finishing Robotic Workcell, which focuses on common surface-finishing tasks like sanding, grinding, and graining.
Cohesive Robotics said it has now combined its software with “best-in-class” robots and welding sources for the Smart Welding Robotic Workcell. “It is capable of performing MIG, TIG, laser, and other welding processes on nearly any part and quantity, with no programming required, thanks to Argus OS,” said the company.
“Our Argus OS simplifies the fixturing and programming process,” explained Pietrocola. “The software scans the work area, finds the part(s), determines the weld areas/joints based on the job setup and recipe configuration, and then performs collision checking and motion planning.”
“So there is no need for traditional teach pendant programming or even cobot hand-guided motion,” he told The Robot Report. “Fixturing is also greatly simplified, and we can handle batch processing of different part SKUs in the same job. Our software also supervises and monitors the job execution and can interface with workcell and auxiliary components such as pneumatic clamps.”
Key features include automatic vision-based detection for common weld joints and tack welds, compatibility with ferrous and non-ferrous metals, and a submillimeter-accurate 3D camera. Cohesive Robotics said its workcell also includes an intuitive human-machine interface (HMI) mobile station.
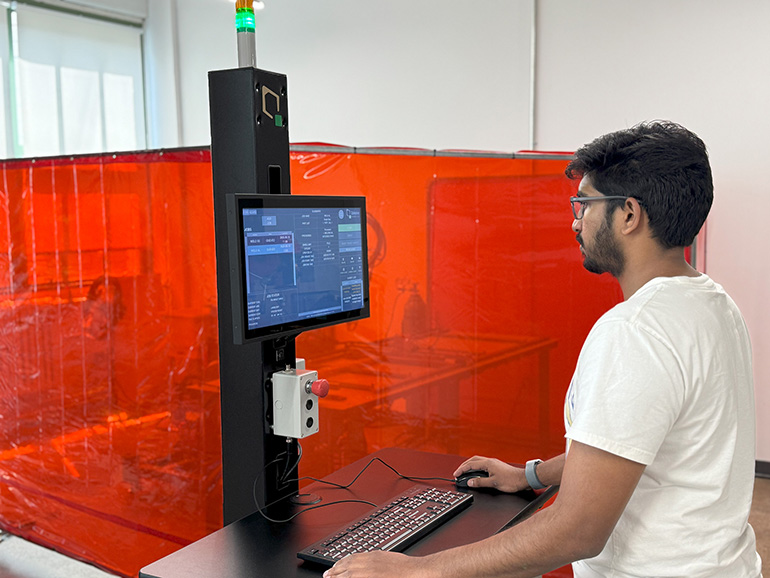
The Smart Welding Robotic Workcell includes a mobile HMI station. Source: Cohesive Robotics
Cohesive Robotics looks to boost productivity
Smart Welding Robotic Workcell can increase production capacity by up to 50% and deliver up to 90% accuracy and consistency, said Cohesive Robotics. This can significantly reduce rework and post-weld cleanup, it asserted.
How much setup does the new workcell require, and how much supervision is needed for workpiece changes?
“We offer a full turnkey solution, which includes installation and commissioning by our team,” Pietrocola replied. “We offer various customization and add-on options as well, such as fixturing design.”
“Regarding workpiece changes, our Argus OS is designed to handle these high-mix environments,” he added. “Depending on how different the part is, adjustments might need to be made for scan positions, fixture design, and/or weld parameters.”
The new system also enables manufacturers to repurpose skilled team members to higher-value tasks by handling tedious, dirty, and dangerous welding operations, according to Cohesive Robotics.